Highly improved sensors, increased computing power and modularisation of products and production enable Western companies to manage the global market despite high production and service costs.
An important part of industry 4.0 is the ever-increasing digitalisation of production that takes place these years. Digitalisation includes many aspects that researchers at DTU Mechanical Engineering contribute to. These aspects are digital monitoring and intelligent use of data, 3D printing and helping companies to think about the product portfolio in modules, so that it becomes faster and cheaper to produce. Common to all aspects is that they are developed in close collaboration between the researchers and one or more companies that can immediately apply the results obtained.
Digital twins
Today, many companies have sophisticated sensors to measure and collect data from their products, both during manufacture, at the final quality control, and in some cases even during use.
“The constant monitoring creates enormous amounts of data. Data that companies must be able to analyse and use intelligently to make their production and development of new products more efficient,” says Professor Jesper Hattel, who heads the work on digitalising industrial production at DTU Mechanical Engineering.
A “digital twin” is the most advanced way of using these data and has already gained ground in several large companies. A digital twin is a digital copy of the entire chain behind a product, from the initial design to the production process itself and to the use of the end product. Digital twins connect the many data from sensors and e.g. 3D scanners with advanced mathematical models of the various manufacturing processes and the physical properties of the materials.
“We are not only dealing with new models, as many of them have already been developed in collaboration with companies over the past 30 years. They contain knowledge of the entire production chain’s behaviour and the physical properties of the materials used. What is new is the quality of the sensors, the models’ increased accuracy, and the addition of the principles of machine learning, so that the models in the digital twins are able to handle and categorise the vast amounts of data collected. In this way, we can create a digital image of the entire company’s value chain,” says Jesper Hattel.
A digital twin makes it possible to simulate changes, both in the manufacturing process and in the final product, and to predict the end result before the changes are implemented in the production hall. At the same time, the digital twin itself is in constant development. Data from the product chain are used to further refine the mathematical models to make the predictions of materials and product properties even more accurate in the future.
3D printing on the way to a new generation
When speaking of digitalisation of production, 3D printing or Additive Manufacturing, which are synonyms for the same family of processes, must also be mentioned. The 3D printing technologies are born digitally and have been continuously improved since the 1990s to make them faster, more accurate and cost efficient.
Today, many companies use 3D printers for the production of prototypes or for smaller production batches. According to Senior Researcher David Bue Pedersen, who heads the research in this area at DTU Mechanical Engineering, the technology will be developed and disseminated much more in the coming years.
“You can say that so far, the development has been about 3D printing in the first generation. In the coming years, we will enter the second generation, where e.g. volume will be of greater importance. The focus will be on printing items in larger sizes and in larger quantities, so that a real 3D print mass production can become realistic,” explains David Bue Pedersen.

Projection of a UV image mask onto the build plane Modularisation can result in huge efficiency improvement and
of the ultra high definition photopolymer Additive the possibility to introduce robotics into the production.
Manufacturing machine at DTU Mechanical engineering.
David Bue Pedersen and his colleagues focus on both 3D printing in plastic and in metal. In relation to the printing of plastic elements, also known as photopoly-merisation, the researchers are working on developing a printer with a resolution that is four times better than that of the market’s existing printers. Such a high resolution makes it possible to work with the surface of the printed elements and add structures to the print as seen on credit cards, for example.
DTU is one of the few European universities to work with the entire process behind 3D printing in metal. Also in this area, the researchers’ goal is to develop better, faster and more cost-effective processes than those used in existing 3D printers. This is done, among other things, by utilising digital twins of the printing process itself.
Modularisation contributes to a more efficient production
A third aspect of digitalisation is about making a com-pany’s processes more efficient. This is achieved by creating an overall overview of the company’s products as a basis for a simplified architecture, where the products’ elements are assembled in modules.
Professor Niels Henrik Mortensen has collaborated with a large number of large and small companies on such processes. As an example, he mentions a Danish manufacturer of hydraulic cylinders that initiated a new project every time a customer approached. This had resulted in more than 80,000 different products over the years. When going over the portfolio with the researchers from DTU Mechanical Engineering, the many products were divided into just 30 different modules, which can be combined in different ways to create the specific type of hydraulic cylinder that the customer demands. The modularisation resulted in a huge efficiency improvement for the company, which, among other things, has been able to introduce robot-ics into the simplified production of the modules.
“We are currently working with another company on a modularisation of their services. When you are in charge of maintenance of, for example, valves in a pro-duction hall, the cleaning takes place one valve at a time, as they become clogged. A few weeks or months later, you therefore have to come back to clean the next valve. This means that production must be shut down in the meantime, at a great cost to the company. We are therefore working on assembling the maintenance in modules, so that a larger group
of valves can be cleaned at the same time, which will significantly reduce the downtime for production,” says Niels Henrik Mortensen.
Based on the work with modularisation, Niels Henrik Mortensen and his colleagues have succeeded in creating the first Product Data Management (PDM) system, which encompasses the entire architecture that a company can create by means of modularisation. PDM is a digital management tool, already used by many companies, which the researchers will develop over the next few years so that it not only includes the architecture, but also the product’s life cycle. This will be based on data from the monitoring of the entire product chain from design and manufacturing, through to final use by the customers, which forms the basis for the entire digitalisation process.
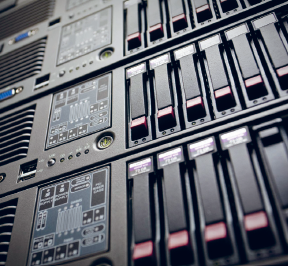
The constant monitoring of productions and
products creates enormous amounts of data.
Less fuel, shorter sailing time and greater safety
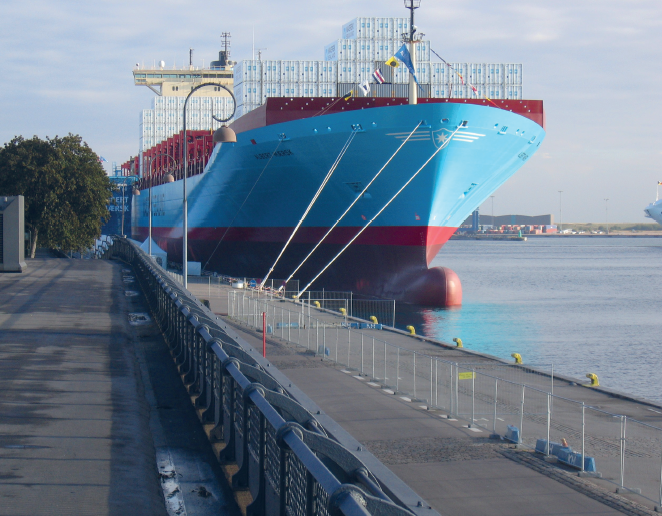
Digitalisation has also found its way into the maritime world. Here, the goal is to have the ships transport their cargo safely and as quickly as possible to their destination, using the lowest possible fuel consump-tion and with least possible emission of particles.
The development takes place in close collaboration between researchers from DTU Mechanical Engineering and companies such as Mærsk, which owns the world’s largest fleet of cargo ships. Mærsk has utilised the technological development to obtain a huge amount of data from their ships, which includes monitoring of engines, hull tension and the accelerations of the ships. These data are supplemented with data from the weather conditions, e.g. waves and wind force, which affect a voyage.
“Ships are complicated structures that operate in probably the world’s toughest environments. Digitalisation has taken place over several years in the maritime world, also in the form of digital twins. However, due to the complex interaction between weather, sea and construction, digitalisation is not without its challenges. Therefore, the industry does not yet have a completely standardised approach for the work with data collected in connection with voyages, for example. This includes both the format to measure the data in, and which data are interesting,” says Associate Professor Ulrik Dam Nielsen, who heads the research in this field at DTU Mechanical Engineering.
Ulrik Dam Nielsen has no doubt, however, that the digitalisation in the maritime world will develop strongly in the coming years. Digitalisation forms the basis for an upcoming full or partial automation of the shipping traffic, which will be implemented both in Denmark and abroad.